銅業知識:銅排表面處理的三種工藝
導讀: 光亮硫酸鹽鍍錫液主要成分為硫酸亞錫和硫酸,生產中其含量隨所采用的添加劑不同而不同。
銅排:又稱銅母線、銅母排或銅匯流排、接地銅排,是由銅材質制作的,截面為矩形或倒角(圓角)矩形的長導體,由鋁質材料制作的稱為鋁排,在電路中起輸送電流和連接電氣設備的作用。銅母線的質量要求執行的是GB/T5585.1-2005標準。
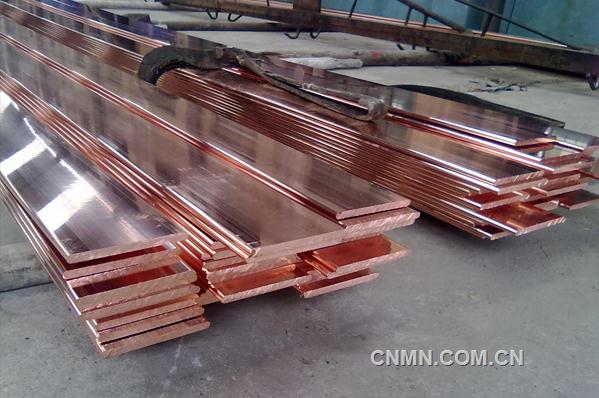
銅排表面處理的三種工藝如下
1.銅排涂漆;
2.銅排鍍錫;
3.銅排涂鍍保護劑;
下面將對這三種工藝作一個全面介紹。
1.銅排涂漆
1.1.此工藝屬于淘汰落后工藝,現很少使用。
1.2.三相交流電路的母線均涂黑漆,在顯眼處粘貼色標,A相為黃色,B相為綠色,C相為紅色,零線或中性線涂淡藍色漆,安全用的接地線涂交替黃綠雙色漆,無法區分極性、相序者涂白漆。
1.3.直流電路的正極涂棕漆,負極涂藍色漆,接地中線涂淡藍色漆。
1.4.檢查母線的涂漆是否均勻,是否有流掛現象。
1.5.母線涂漆可采用噴漆或刷漆,色澤應均勻,邊緣應整齊,不得有漏漆、掛漆現象,母線連接處不得沾漆。
1.6.同一元件,同一端的各相母線的涂漆界線應無明顯不整齊現象。
1.7.母線的涂漆界線平齊。
2.銅排鍍錫
2.1.工藝成熟.操作周期短,普遍采用。
2.2.弱點:時間長了表面發暗,人手做不到。不環保!
2.3.工藝流程
2.3.1.表面拋光除油等前處理→純水洗→鍍高Pb-Sn合金個自來水洗→純水洗→鍍錫→自來水噴洗→中和(Na2HPO4+Na3PO4)→自來水噴洗→浸硬脂酸→自來水噴洗→熱純水浸洗→烘干。
2.4.銅排表面處理工藝拋光:無論是人工還是機械都慢,而且累,粉塵很嚴重,清理表面氧化皮,微小毛刺。(用石英砂,玻璃丸)。
2.5.鍍液各成分作用及工藝流程
2.6.光亮硫酸鹽鍍錫液主要成分為硫酸亞錫和硫酸,生產中其含量隨所采用的添加劑不同而不同。
2.6.1.硫酸亞錫為主鹽,含量十般控制在40~100g/L。但生產實驗結果表明,高濃度硫酸亞錫雖然可以提高陰極電流密度,加快沉積速度,但使鍍液分散能力明顯下降,且使鍍層結晶粗、光亮區域變小,甚至大大縮短了鍍液的處理周期。
2.6.2.SnSO4含量控制在20~60g/L為宜,若取下限,可以通過加快鍍液循環速度及電極(陰極或陽極)移動速度等辦法進行“補償”,仍可鍍出優良產品,但不宜過低。
2.7.硫酸具有降低亞錫離子的活性、防止其水解、提高鍍液導電性能及陽極電流效率等作用。當硫酸量不足時,亞錫離子易氧化成四價錫。
2.8.從動力學的觀點分析,當有足夠的H2SO4時,可以減慢二價錫的水解,穩定鍍液,實際生產中H2SO4含量一般在80~150mL/L。
2.9.添加劑
2.9.1.鍍錫光亮劑一般是由主光劑、輔助光亮劑、載體光亮劑復配制成。
2.9.2.主光劑
2.9.3.酸性光亮鍍錫光亮劑的種類繁多,歸納起來可分為兩大類:第1類主要是芳醛、芳酮、酯類及不飽和有機酸烯的衍生物,第2類主要是西佛堿類 (基本結構單元為-CH=N—CH=CH-或-CH=CH-CH=N-),由乙醛與鄰甲丙胺縮合而成,是酸性光亮鍍錫有效的增光劑,能單獨使用,也可與第 l類光亮劑配合使用,當與第1類光亮劑配合使用時,能顯著拓寬光亮區,有效消除鍍層白霧。
2.9.4.有機光亮劑的光亮作用主要表現為在陰極上的吸附,陰極上的吸附過強或過弱均無法獲得理想的光亮鍍層。因為吸附太強,脫附電位太負,析氫嚴重,易形成針孔;吸附過弱時,脫附電位相對較正,鍍層結晶粗糙。只有適當的吸附才能達到好的光亮效果。
2.9.5.所以,在配制組合光亮劑時,應將吸附過強、適當和過弱的添加劑有機配合使用,以達到吸附適度、吸附電位范圍較寬的目的,且各項組合量由實驗確定。目前可用作主光劑的有:芐叉丙酮、枯茗醛、二苯甲酮、O—氯苯甲醛等,其中芐叉丙酮常用。
2.9.6.輔助光亮劑
2.9.7.因為主光劑均只能在某一電流密度范圍內發揮光亮作用,所以單獨使用是不能獲得理想鍍層的,但是如果和輔助光亮劑配合使用就能起到協同效應, 從而使鍍層結晶細化、光亮電流密度區域進一步擴大。屬于這類添加劑的是脂肪醛和一些有機酸類,常用的有甲醛、丙烯酸、肉桂酸等。
2.9.8.載體光亮劑
2.9.9.大多數有機光亮劑在水中的溶解度非常小,因而在陰極上被吸附的量也少,所以不宜單獨加入鍍液;有些有機光亮劑在電鍍過程中因發生氧化、聚合 等反應,容易從鍍液中析出。因此,如果要使光亮劑的效果得到充分發揮,就必須加入一些表面活性劑,利用其增溶作用來提高光亮劑在鍍液中的含量,這些表面活 性劑稱為載體光亮劑,亦稱為分散劑。同時它還具有潤濕和細化結晶等功能。
2.9.10.最早使用的載體光亮劑是一些陰離子表面活性劑,但是它們在陰極上的吸附較弱。后來又開發出非離子型表面活性劑,如聚氧乙烯、聚氧丙烯醚 等,它們既具有潤濕分散作用,又具有抑制H2析出及Sn2+放電而使鍍層晶粒細化的作用。在上述分散劑中,OP乳化劑使用廣泛。
2.10.穩定劑
2.10.1.以硫酸亞錫為主鹽的酸性鍍錫液連續工作半個月就會發生混濁,難以鍍出合格產品,需加一定穩定劑。
2.10.2.常用的酸性鍍錫穩定劑大多是Sn2+的絡合劑,如草酸、檸檬酸、酒石酸等,且復配比單獨使用效果好。另外,某種催化劑也有穩定鍍液的作用,生產表明,在連續生產的情況下,加入這種催化劑的鍍液能保持半年以上的時間清亮不濁。
2.11.絮凝劑
2.11.1.至今還沒有一種穩定劑:能長期保持鍍液穩定、清澈透明,因此Sn4+不可避免產生。隨著Sn4+的積累,鍍液逐漸變渾,沉渣增加,鍍層光亮區變小、均勻性變差,甚至出現發暗、發花等現象,此時必須對鍍液進行絮凝劑處理。
2.11.2.絮凝劑分無機和有機兩類,無機絮凝劑有各種鹽類、活性硅土等,有機絮凝劑可分為陰離子、陽離子、非離子3種。陰離子型絮凝劑主要有環氧胺 系共聚物、聚乙烯亞胺、聚乙烯胺類衍生物等,陰離子型絮凝劑主要有聚丙烯酰胺水解物、聚丙烯酰胺、磺酸鈉類等,非離子型絮凝劑主要有聚丙烯酰胺、脲—醛聚 合物等。
2.11.3.聚丙烯酰胺和無機絮凝劑配合使用效果非常好,對鍍液的性能無任何影響,但沉降速度太慢,長達48h以上。環氧胺系共聚物的效果較好,但過 量使用對鍍液有一些影響,嚴重時影響鍍層光亮度,但沉降速度特別快,一般在2h之內可完全沉淀下來(使用時切忌過量)。
3.銅排涂鍍保護劑
3.1.優點:維持銅排原色,比鍍錫成本略低。缺點:操作周期長。
3.2.工藝流程
3.3.拋光前處理→純水洗→酸洗鈍化工件→烘干水分→JLR-510保護處理→流動水洗干凈→熱水浸泡(100℃左右,要用于工件升溫,目的是讓水分自行揮發或者干燥)→烘干→包裝封閉
3.4.銅排表面處理工藝拋光:無論是人工還是機械都慢,而且累,粉塵很嚴重,清理表面氧化皮,微小毛刺。(用石英砂,玻璃丸)。
3.5.酸洗鈍化的主要流程為:前處理(凈化表面)→酸洗鈍化及沖洗→后處理(成品保護)。前處理的主要內容是凈化酸洗、鈍化物件的表面,清除表面的各 種油脂、焊接飛濺、焊疤、氧化皮等。酸洗、鈍化可以將酸洗、鈍化分開處理,也可以將酸洗、鈍化合二為一同步進行處理。將酸洗、鈍化分開處理時,多采用將工 件整體浸泡在酸洗鈍化液中的方式,適合于小型零部件或內部可以進行液體循環的管線、線形設備。將酸洗鈍化合二為一處理時,可以采用液體浸泡方式(適合范圍 同上),也可以采用膏體進行涂抹,由于膏體涂抹方便,在不同位置都可以保持較長時間不流失及潤濕性,從而保證了酸洗鈍化必要的時間。
3.6.銅件防氧化保護劑JLR-510
銅件防氧化保護劑性能穩定,無毒、無味、不揮發、不潮解、不分解、不升華不吸附灰塵及H2S、、、SO2等害氣體,能夠有效抵制濕熱鹽霧、霉菌等對金屬 的侵蝕,有較好的潤濕性和較高的抗蝕性能。。銅件防氧化保護劑電氣性能也極佳,而且具有脫水、防變色、防銹蝕三重作用,對金屬沒有腐蝕作用,對銅、銀及仿 金鍍層有明顯的抗蝕防護作用,,尤其對防止銅和仿金表面變色,效果顯著。本產品還可以加入其他助劑中配合使用,例如水性、溶劑性的封閉劑、罩光金油、防銹 劑等產品,對于銅、金、銀、鋅、鋼鐵等金屬的防銹起到不可估量的作用。
3.7.容器建議選用各種塑料容器,不得選用金屬容器,除非是銅質容器。然后將JLR-510銅件防氧化保護液直接使用。
3.8.本工作液可以在常溫下和加溫的情況下進行保護,但是建議在加溫條件下使用,這樣生產效率更高,而且效果更好。但是加溫的方式宜選擇合理的加溫方 式,如果采用內置方式,加溫管一定要是銅質的,或者采用石英及聚四氟乙烯(特氟龍)加熱管,如果是其他金屬材質的加熱管,將改變藥液的性能,不宜采用。
3.9.使用方法:
3.9.1.工件經過除油后化學拋光與清洗?B、電鍍光亮酸銅或其它銅出來后;選用流動水漂洗兩次,再用去離子水清洗一次(這樣可以使藥液中盡可能帶入更少的雜質,從而延長藥液的使用壽命);
3.9.2.如果是在常溫情況下操作,一定要在工作液中處理5-10分鐘,原則上不得低于5分鐘,因為在室溫下,本液在銅層所形成的鈍化膜會在5分鐘左右,如果產品要求鹽霧實驗高于8小時,建議在加溫情況下使用;
3.9.3.如果是在加溫的情況下使用,建議溫度控制在60-70℃之間,最好在65℃左右,在這種條件下,銅件防氧化保護只要2分鐘(建議處理時間在3分鐘)就能形成完整而均勻且有光澤的保護膜層,達到最佳的防變色效果。
3.9.4.通過上述方式處理以后,用流動水洗1分鐘,甩干至工件表面無水珠,取出在70-80℃的溫度下烘干或者擦拭干表面的水珠即可。
3.10.槽液維護:
3.10.1.工作液的壽命很大程度上取決于工作前清洗干凈程度。經酸洗的零件要水洗干凈,不能有殘酸帶入鈍化液中。(溶液酸度增高,使銅件上的膜層溶 解,起不到防護作用。)因此,鈍化液要與酸洗溶液分開,避免六價鉻、三價鉻離子的進入,而且復雜產品進入防變色槽中前,要避免有殘余的藥液存在,長期如 此,才能使溶液的壽命達到最佳狀態。
3.10.2.設備的選用:設備的選材至為關鍵,容器一般以塑料為主,加溫管必須是銅材的,或者選用外置的加熱方式(可以由我公司提供相關的設計與溫控裝置)。
3.10.3.不要讓其它金屬零件進入溶液中。
3.10.4.溶液壽命的判斷一般以PH值為標準,新配槽液PH值一般為6±1,近中性,當溶液PH超出6-7±3時,溶液應予以報廢,如果防變色要求 時間不高,可以以試驗為標準,一般情況下,本液在PH2-9的情況下都是有良好鈍化作用,如果質量要求高的時候,可以將PH控制在5-7和4-8的范圍以 內。
3.10.5.另外,防變色槽液前的請水槽需要經常用PH試紙檢查其PH數值,如果發現清水脫離中性,建議立即更換請水,否則防變色劑將受到影響。五、廢水處理:本產品廢液可以直接排放。
3.11.銅保護鈍化液性能測試數據:處理條件:銅件防氧化保護溶液,溫度65-70℃,時間2分鐘。對比條件:傳統鉻酸處理品。
樂清市人禾電子有限公司是浙江最好的銅排廠家,專注于新能源電動車電池銅排連接、電工連接銅排、編織銅排、軟銅排連接、線纜連接以及絕緣保護套生產、研發和銷售。產品符合歐盟環保、UL阻燃,ISO9001管理體系認證要求。